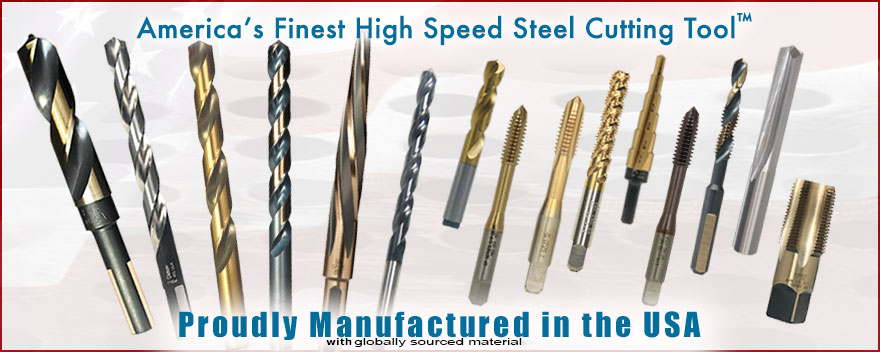
Consolidated Toledo Drill
Common Drill Issues
Drills are the most used, Misunderstood & Abused tools in metal removal operations.
Drill Choices — Bolt holes, holes for inserting Wood screws, Rivet holes and other common hole drilling require
no more hole preparation than that imparted by the drill itself. But in cases where fits in the hole need to be close,
screw or bolt heads need to be flush or where the hole is to be threaded, choice of the drill is critical.
This is more important when drilling is a repetitive production-rate operation or the drill is fed automatically
to the hole site in a tool changer.
Drills do not cut precisely to size, other round hole, secondary operation tools are recommended for refinishing,
resizing, or reworking the hole: drills for enlarging the hole,
Countersinks or Counter bores for flush screw or Bolt heads,
Reamers for refinishing & resizing the hole.
VARIABLES:
-
• Hole Size — feed and speed must not exceed
drill’s structural strength.
• Blind or through hole — chips may clog in a blind and bind and break the drill; Excessive feed may cause the drills edges to catch and break as they reach the end of the through hole.
• Rigidity of the Work & Drill — checking lateral forces on the drill maintains concentricity and avoids strains on the flutes, edges and body.
• Centering as the Drill Contacts the Work — drill point angles must be similar so the drill seats precisely at contact.
• Chip Formation & Clearing — split points and other design features including proper flute helix enhance chip removal
• Desired Finish — a function of point geometry, drill concentricity and ductility of the work-piece material. Core drills enlarge and improve finishes in existing holes.
• Drill Mountings — vary widely from chucks to adapters. They must seat the drill shank securely and precisely centered to avoid run-out.
• Metal Lubricant / Coolant — enhances tool life and yield a super machined finish.
Cause:
1. Shank or Socke Damaged 2. Twist Drill Not Properly Seated In Socket
Correction:
• Repair or Replace • Check For Positive, Secure Fit
Cause:
1. Insufficient feed 2. Improper style of drill and/or point
Correction:
• Increase Feed
Cause:
1. Using Hard Object To Tap Drill Into Socket 2. Dropping, Mishandling Drill Bit
Correction:
• Use Soft Lead, Plastic, etc... Hammer • Handle With Care
Cause:
1. Drill Point Off–Center 2. Machine Spindle Not Rigid or Not Running True 3. Work Piece Loose and/or Vibrating
Correction:
• Re–point Accurately or Replace with Properly Pointed Drill • Repair if Possible; Consider Use of Bushing
• Tighten & Hold securely
Cause:
1. Incorrect Point Grind and/or Dull Drill 2. Excessive Feed 3. Incorrect or Insufficient Coolant
Correction:
• Re–point or Replace with Properly Pointed Drill • Reduce Feed • Correct & Adjust
Cause:
1. Coolant Not Reaching Drill Point or Insufficient or Incorrect Coolant
2. Speed Too High and/or Feed Too Low 3. Wrong type of point and/or drill for application
Correction:
• Correct & Adjust • Review & Adjust • Review Requirements & Conditions
Cause:
1. Insufficient Lip Clearance 2. Point Thinned Too Much 3. Excessive Feed
Correction:
• Repoint or Replace With Properly Pointed Drill • Repoint or Replace With Properly Pointed Drill • Reduce Feed
Cause:
1. Excessive Lip Clearance and/ or Heel Relief
Correction:
• Repoint or Replace With Properly Pointed Drill
Cause:
1. Large Run Out After Attached to Machine, Loose Holder 2. Cutting Speeds or Feeds Is Too High
Correction:
• Check Holder and/or Select Another Holder • Reduce Cutting Speeds or Feeds
Cause:
1. Insufficient or Incorrect Coolant 2. Excessive Speed 3. Scale, Hard Spots Encountered In Material
Correction:
• Correct & Adjust • Reduce Speed • No Final Remedy. If This Condition Is Prevalent; Lower Feeds and Speeds May Help
Cause:
1. Flutes Clogged With Chips, Drill Binds In Hole (Common in deep holes) 2. Drill Binding Due to Worn Outer Corners
3. Work Insecurely Held 4. Excessive Feed
5. Improper Point 6. Twist Drill Is Dull
Correction:
• Use A Drill With Wider Flutes and/or Faster Helix Angle
• Consider Polished Flutes
• Withdraw Drill at Regular Intervals To Clear Chips
• If Chips Are Not Broken Up, Consider Heavier Feeds.
• Repoint or Replace Drill Bit
• Check For Excessive Speed, Inadequate or Incorrect Coolant, Excessive Run Out As Drill Enters Work Material
• Use Adequate Holding or Clamping Devices
• Reduce Feed
• Check For Correct Lip Clearance
• Use Proper Type Of Drill & Point For The Application
• Replace Before Dulling Occurs. Check Feeds, Speeds & #5 For Premature Dulling